Process maintenance & Quality (PMQ)
Process Maintenance and Quality (PMQ)
The Process maintenance and quality division (PMQ) covers all the trades that are essential to the process, quality and maintenance business; it is involved in the implementation of technical and organizational solutions aimed at achieving the set cost, quality and deadline objectives:
It intervenes from the feasibility study, implementing an organization and project management in accordance with the ISO 10006 standard.
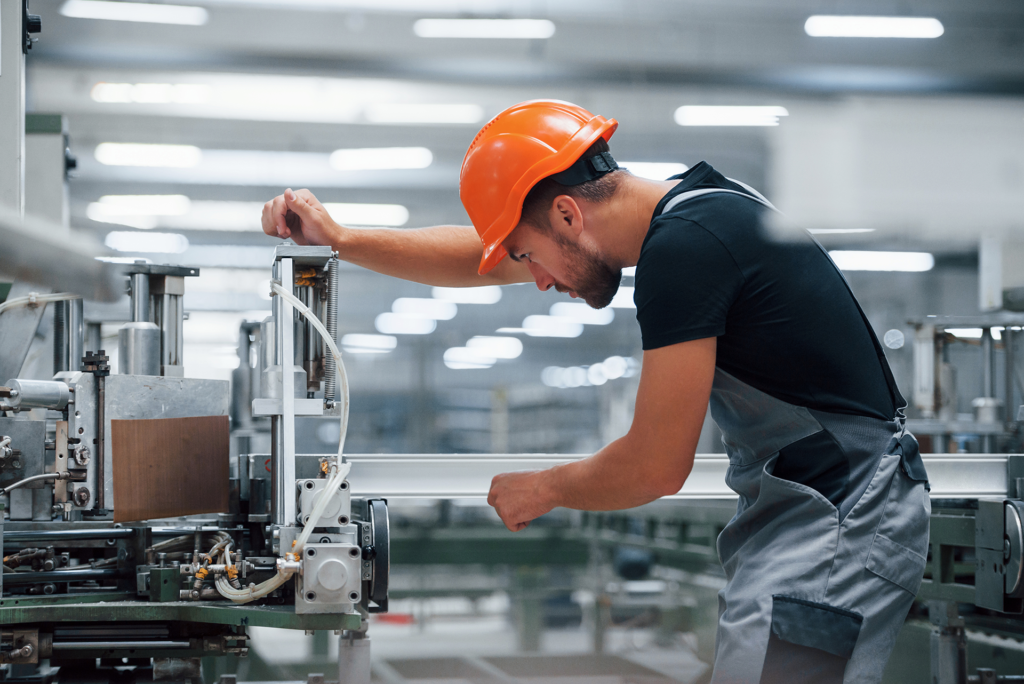
Our method/manufacturing professions
- Transfer of production between sites and increase in production rate
- Assembly studies
- Studies and validation of tools (molds,…)
- Formalization of customer expectations, understanding of the process environment
- Audits and diagnoses based on the 5Ms: environment, material, means, method, manpower
- Machine capability studies
- Improvement of product and process FMEAs.
- Synthesis, proposals and validation of solutions with the operational staff
- Implementation of agreed solutions, including MSP monitoring system
- Training of operational staff
- Continuous measurement of process performance changes.
- Qualification/validation/certification (QI,Q0,QP) of processes
Our quality professions
Project Management:
- Ensure the effective management of new product/process development projects
- Conducting the project prescribed by the manufacturers planning quality for new products
- Application of reference tools and automotive/aeronautical and defense standards (FMECA, MSP, MSA, PPAP/PPA…)
- Monitor performance indicators: project quality/cost, deadline, schedule, delivery.
Continuous Improvement:
- Management of continuous improvement projects:
MUDAS HUNTING / STOP SCRAP /HOSHIN… - Achieve gains by reducing non-quality costs (NCQ) and optimizing cycle times
- Implementation of quality basics
Supplier Quality Assurance :
- Audits & risk studies of suppliers
- Evaluation of suppliers based on PPM and claims performance
- QRs challenge, PDCA-FTA of suppliers
- Preparation of ” charge back supplier ” files
- Support and follow-up of action plans (8D, PDCA) following non-compliance
Customer/Operational Quality Assurance:
- Mastery of the QRQC tool
- Mastery of quality tools: FMEA / 5 WHY / ISHIKAWA / PDCA-FTA / PSQ / 8D …
- In-depth knowledge of customer requirements/specifications.
- Knowledge of standards: ISO 9001 /ISO14001-45001/ISO TS/IATF 16949 / EN 9100 /ISO26262 / NADCAP certification /…
Project Quality Assurance:
- Ensure customer requirements (STE PSA/QSB Plus,…)
- Preparation of FAI & PPAP files
- Ensure the APQP process & preparation of customer audits
- To manage and update the process FMEA;
Our maintenance professions
- Predictive maintenance
- Curative maintenance
- Equipment qualification testing and reporting procedures
- Security system
- Prediction with statistics
- Definition of optimal intervention times
- Inspection schedule
- Installation of sensors & measurements
- Data analysis
- Evaluation of costs